Receiving your products at Green Fulfilment
Seamless Inventory Intake: Streamlining Your Goods In Process
The Goods In process is your gateway to efficient order fulfilment. This is where we receive your stock, whether by loose cartons, pallets, or container loads. Accuracy is paramount, as any discrepancies can affect your inventory levels and order fulfilment.
Green Fulfilment makes receiving your stock a breeze.
- Real-time tracking: Our system provides you with live updates on the status of your incoming goods, keeping you informed every step of the way.
- Automated notifications: Stay effortlessly in the loop with system-generated messages from the Green Portal, ensuring you’re always aware of the progress.
- Inventory accuracy: Our meticulous receiving process minimises errors, guaranteeing your inventory reflects reality for smooth order fulfilment.
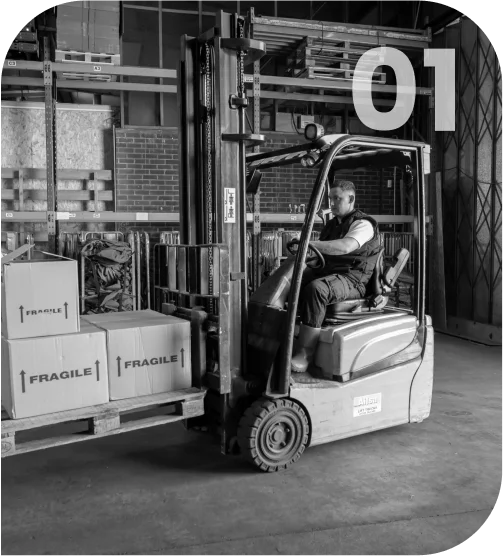
How does goods in work?
Dive Deeper into Goods In: A Streamlined Process
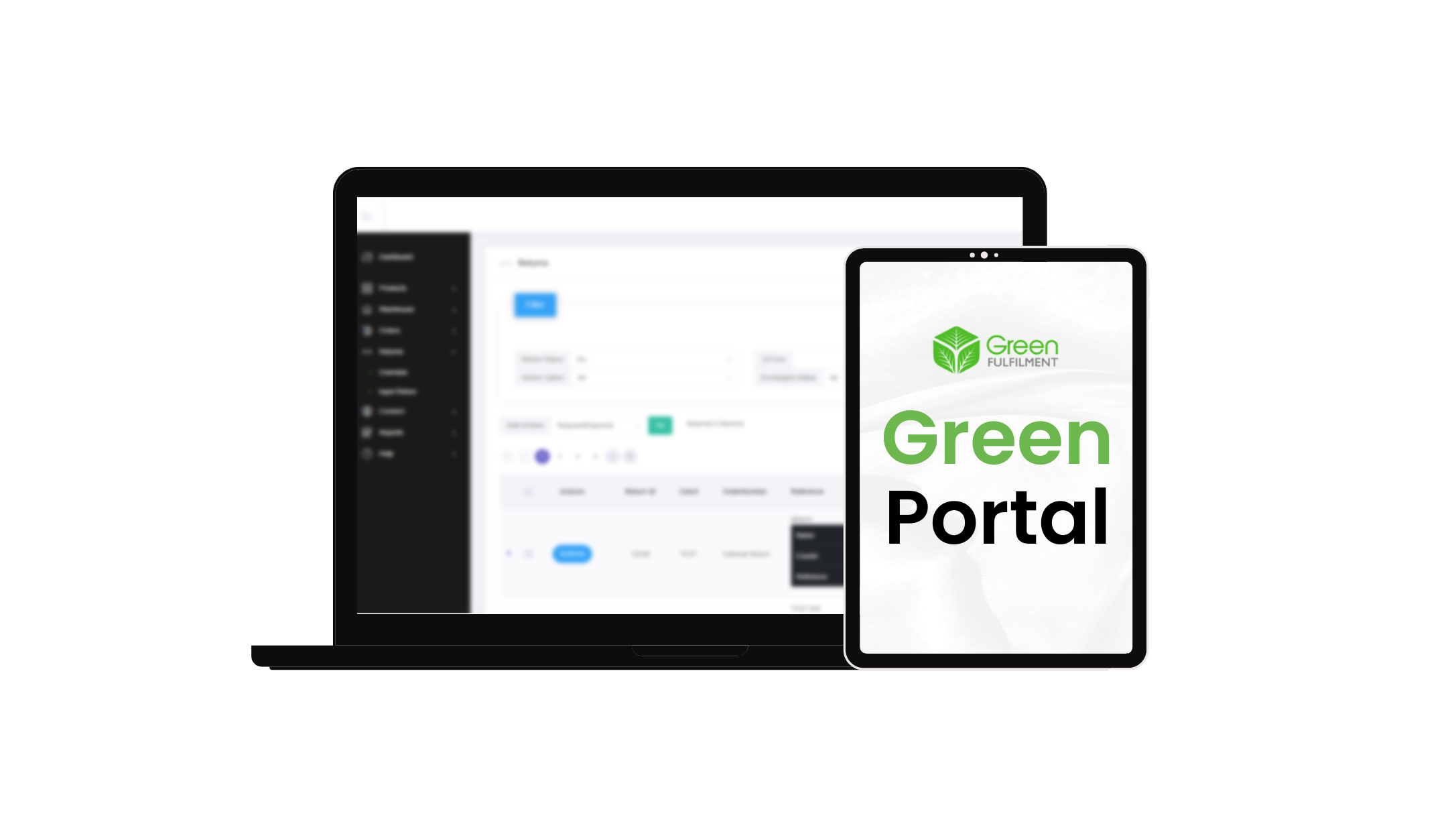
Getting Started: Account and Product Setup
Before your first shipment arrives, our onboarding team will ensure everything is set up for a smooth transition. This includes:
- Account Creation: Your dedicated onboarding manager will create an account for you in the Green Portal, your one-stop shop for real-time inventory updates and order management.
- Product Creation: We’ll work with you to create detailed product data (SKUs) within the Green Portal, ensuring accurate tracking.
Coordinating Your Shipment
Once your SKUs are entered into the system, you’ll inform us of the specific products and quantities you’re sending and schedule a delivery date with your onboarding manager. This information is then logged in the Green Portal as an Advance Shipping Notification (ASN).
We can even assist with arranging pickup from your current location if needed.
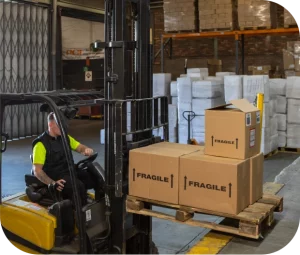
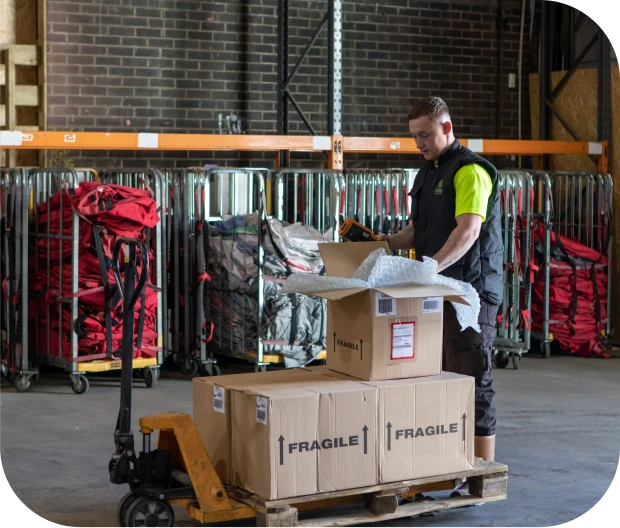
Seamless Receiving and Inventory Management
Upon arrival at our fulfilment warehouse, our Goods In team uses your ASN as a reference to verify received items. Products are then segregated for further inspection.
- Visual Checks: Our team performs a visual quality check to ensure no obvious damage.
- Inventory Counting: Each SKU is meticulously counted using handheld scanners for complete accuracy.
- Strategic Warehousing: Counted stock is then strategically placed within the warehouse based on size, volume, and expected order demand. Location data is captured in the Green Portal to facilitate efficient picking for customer orders.
The Green Fulfilment Advantage
Throughout the Goods In process, you have complete transparency through the Green Portal. Live updates keep you informed at every stage, ensuring your inventory is safe, secure, and ready to meet your customer needs.
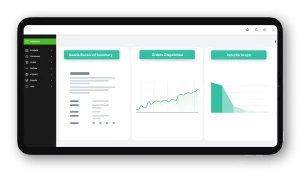
Join the Green Fulfilment Movement: See How Brands Achieve Success

“Green Fulfilment are a company that care about their customers. They are very flexible, provide great service and when we face supplier issues they work hard to turnaround our shipments.”
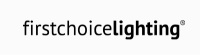
“Green have been our fulfilment partner for many years and have demonstrated excellent value and efficiency throughout. They are an integral part of our business and we greatly value our alliance and trading relationship. “
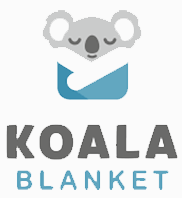
“Great partners…we have grown very fast almost at the same time as we moved to Green and they have not let us down…I would recommend them to other brands who are looking to grow.” – Chris Katona
Learn more about our order fulfilment process
Green Fulfilment offers a one-stop shop for all your order fulfilment needs.
We efficiently manage every stage – from receiving inventory to shipping and returns – ensuring a smooth and stress-free experience.
Contact Us
Achieve Your Growth Goals - Talk to Us Today!
Connect with a fulfilment expert to unlock your growth potential! They’ll schedule a free consultation to discuss your current operations, ambitious goals, and any challenges you’re facing.
Frequently Asked Questions
Why do I need an inventory management system?
An inventory management system (IMS) is important no matter how big or small your business is. It’s a tool for effectively managing stock levels, optimising operations, and improving profitability. And here’s why:
- An IMS does accurate inventory tracking. It provides real-time visibility into inventory levels, preventing stockouts and overstocking.
- Efficient inventory management leads to faster order fulfilment and with less errors.
- An IMS optimises inventory levels, reduces carrying costs, and minimises the risk of obsolescence.
- IMS provides data-driven insights for better purchasing, production, and pricing decisions.
- An IMS helps ensure compliance with industry regulations and standards.
How should inventories be managed?
Effective inventory management usually involves accurately predicting future demand to avoid stockouts or overstocking. Inventory optimisation also comes into play, where the fulfilment centre balances inventory levels to meet customer needs while minimising costs.
Regular audits — physically checking inventory — are also done to verify accuracy and identify discrepancies. To do it effectively, fulfilment centres utilise inventory management software to automate processes and gather insights.
It’s also best to maintain a collaborative relationship with your suppliers to make sure all deliveries are made on time and to optimise inventory levels. And on top of that, regularly reviewing and refining inventory management practices are also needed to maintain, and even enhance, efficiency.
What is the ideal inventory process?
The ideal inventory management process involves accurately predicting future demand based on historical data, market trends, and other factors. After using data to make informed decisions, orders are then placed with suppliers and inventory is received upon arrival.
The fulfilment centre staff handles storing products in designated locations and organising them efficiently. To track inventory accurately, most fulfilment centres use barcode scanning or RFID technology.
When customers place their orders, the staff handles the picking, packing, and shipping. All of the orders are handled according to customer demand. And when stocks are running low, placing orders to replenish stock levels come next. This is based on reorder points and demand forecasts.
In addition to efficiently processing orders, regular inventory audits are also conducted to verify accuracy and identify discrepancies. And as the process continues, inventory data is continuously analysed to identify areas for improvement and make necessary adjustments.
What is the most common method of inventory control?
The most common method is periodic review. This involves physically counting inventory at regular intervals (e.g., monthly, quarterly) and comparing the results to recorded quantities.
Other methods of inventory control are:
- Continuous review: Constantly monitoring inventory levels and placing replenishment orders as needed.
- ABC analysis: Categorising inventory items based on value and usage to prioritise management efforts.
Do you charge for restocking?
Yes, we do. Restocking fees are usually based on the number of items restocked, the complexity of the process, and the frequency of your restocking requests. Restocking fees help cover the costs of labour, storage, and handling associated with returning and re-storing products.
To get an exact idea for how much your business needs to pay for restocking, we recommend reaching out to the team at Green Fulfilment for personalised pricing and support.
How can I track my inventory?
Our software, Green Portal, gives you complete transparency through live updates. You’re informed at every stage of inventory management and you can be assured that your stock is safe, secure, and ready to meet your customer needs.
We can help you track your inventory levels in real-time, monitor stock levels, identify slow-moving items, and stop you from losing sales because of stockouts.