Green Fulfilment: Pick & Pack with Precision
The Heart of Efficient Order Fulfilment
The pick and pack process is the backbone of any successful fulfilment operation. At Green Fulfilment, we understand its critical role in delivering exceptional customer experiences. Here’s what sets us apart:
Unmatched Accuracy: 99.99% Pick Rate Guarantee
We take pride in our industry-leading 99.99% pick accuracy rate. This is achieved through a powerful combination of:
- Technology: Our Green Portal guides pickers using handheld scanners, ensuring they follow the most efficient routes and pick the correct items every time.
- People: Our dedicated team is highly trained and supported by technology, minimizing errors.
- Processes: We continuously refine our processes for speed, accuracy, and consistency.
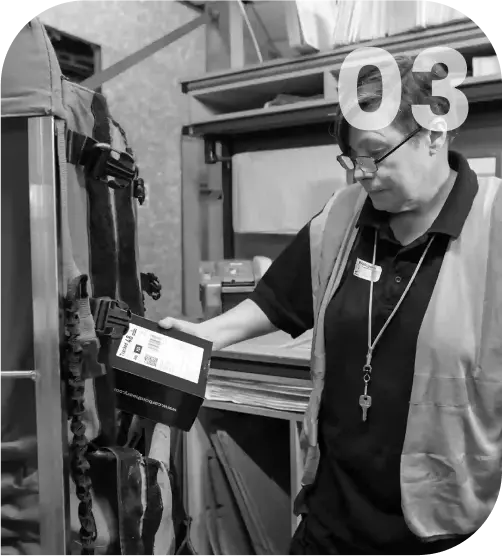
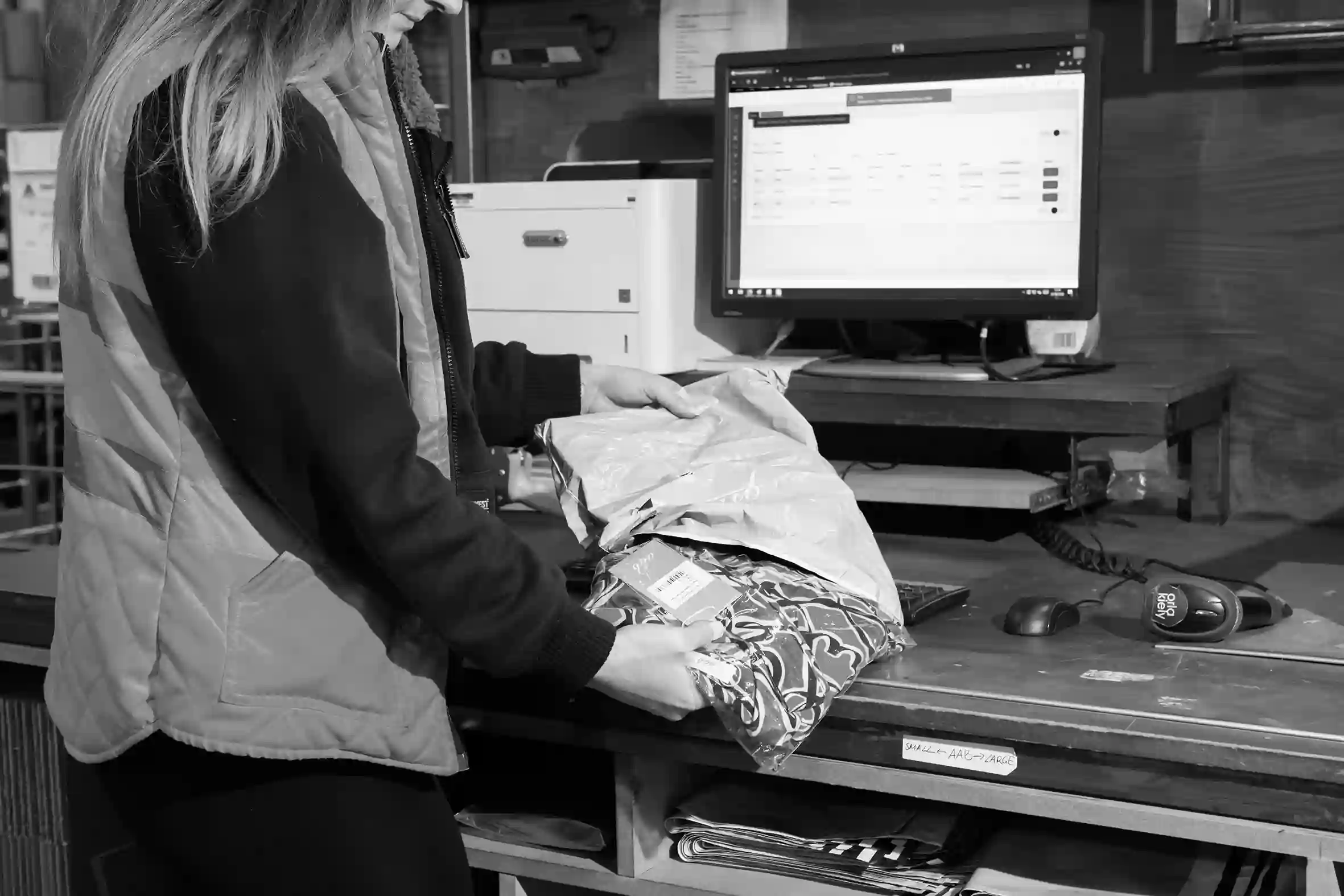
Sustainable Packaging Solutions
We believe in responsible practices and offer eco-friendly packaging options:
- Right-sized boxes: We use the perfect box size for each order, reducing waste and unnecessary void fill.
- Paper-based materials: We say no to plastic! Our packing stations are stocked with paper tape, paper void fill, and compostable mailers made from sugarcane.
- Durable paper mailers: Our customers love the surprising strength and weather resistance of our paper mailers.
People and Technology in Harmony
Our technology seamlessly integrates with our experienced team to achieve optimal results:
- Paperless Picking: We save paper and boost efficiency by using the Green Portal for order picking instead of printed lists.
- AI-powered Optimization: Our AI technology guides pickers along the most time-saving routes within the warehouse.
- Ergonomic Packing Stations: Our packers have everything they need within reach, ensuring a smooth and efficient packing workflow.
- Standardised Processes: Consistent processes across all our warehouses guarantee a seamless experience regardless of location.
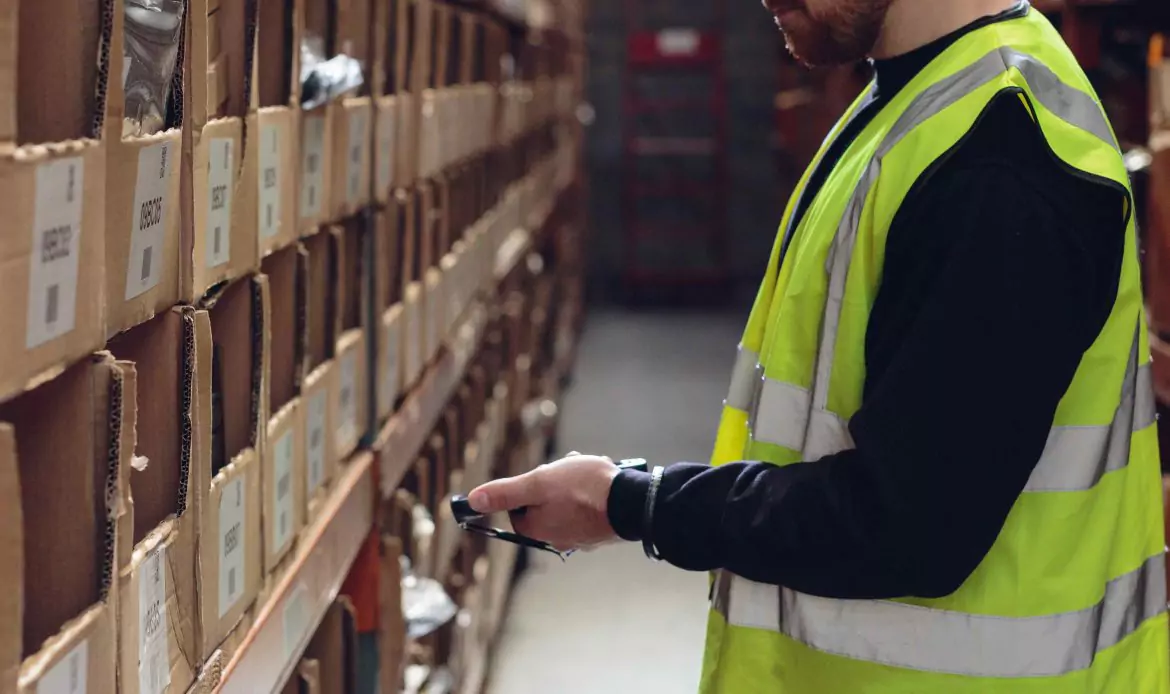
Join the Green Fulfilment Movement: See How Brands Achieve Success

“Green Fulfilment are a company that care about their customers. They are very flexible, provide great service and when we face supplier issues they work hard to turnaround our shipments.”
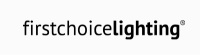
“Green have been our fulfilment partner for many years and have demonstrated excellent value and efficiency throughout. They are an integral part of our business and we greatly value our alliance and trading relationship. “
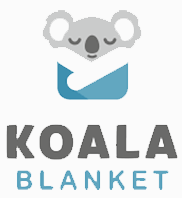
“Great partners…we have grown very fast almost at the same time as we moved to Green and they have not let us down…I would recommend them to other brands who are looking to grow.” – Chris Katona
Learn more about our order fulfilment process
Green Fulfilment offers a one-stop shop for all your order fulfilment needs.
We efficiently manage every stage – from receiving inventory to shipping and returns – ensuring a smooth and stress-free experience.
Frequently Asked Questions
What is the difference between picking and packing in a warehouse?
Picking and packing services are two different processes, but they are interconnected in warehouse operations. Together, they form the core of order fulfilment.
Picking involves locating and retrieving specific items from storage based on customer orders. The staff collect the correct products in the right quantities and move them to a staging area. It focuses on accuracy and efficiency in the retrieval of items.
Packing is when the picked items are prepared for shipment. This includes placing products in appropriate packaging materials, sealing the package, and affixing the right shipping labels. This is the process that focuses on protecting the products during transit and preparing them for shipment.
What are the two primary picking strategies in a warehouse?
In a fulfilment warehouse, there are two primary picking and packing services and strategies that fulfilment centres implement:
Single-order Picking
This method involves picking all items for a single order before moving on to the next. The order picker fulfils one complete order before moving on to the next. They pick all items for a single customer in one go.
It’s a method that delivers high order accuracy due to focused attention on one order at a time. It’s suitable for smaller order volumes or when handling high-value items. The disadvantage is that it can be less efficient in terms of travel time as the picker may need to traverse the warehouse multiple times for a single order.
Batch Picking
This is when multiple orders get picked simultaneously. Items for different orders are grouped together based on their location in the warehouse.
Batch picking improves efficiency by reducing travel time, which makes it ideal for high-volume order fulfilment. The con is that there is an increased risk of order picking errors due to handling multiple orders at once. It also requires additional sorting and allocation steps after picking.
The choice between single-order picking and batch picking depends on factors like volume, order profile, warehouse layout, and desired level of accuracy. Many warehouses use a combination of both methods to optimise efficiency and accuracy.
Technology also plays a crucial role in order picking. Systems like pick-to-light, voice picking, and automated guided vehicles (AGVs) can significantly enhance the picking process, regardless of the strategy used.
What is bulk picking?
Bulk picking is a highly efficient order picking strategy that involves collecting multiple units of the same product in a single trip to fulfil multiple orders. This is very effective for products with high demand and consistent order quantities.
Bulk picking reduces travel time within the warehouse as pickers only need to visit a storage location once for multiple orders and increases the number of items picked per hour due to fewer trips and reduced idle time.
For example, if there are five orders for ten units of a particular product, bulk picking would involve picking 50 units of that product at once, rather than picking ten units five times.
What is the packing process in a warehouse?
The packing process involves preparing products for shipment and it usually includes the following steps:
- Selecting the packaging material. Choosing whether the item is suited for packing in boxes, fillers, envelops, etc., based on product size, weight, and fragility.
- Carefully placing products in the packaging to prevent damage during transit.
- Using cushioning materials (bubble wrap, packing peanuts, etc.) to protect fragile items during transit to a customer’s doorstep.
- Closing the package securely to prevent tampering or product loss.
- Affixing shipping labels and any necessary documentation to the package.
What are the benefits of outsourcing pick and pack fulfilment?
Outsourcing picking and packing services, often through a third-party logistics (3PL) provider, gives businesses like yours several advantages:
- More time to focus on core competencies: Allows businesses to concentrate on product development, marketing, and customer acquisition.
- Cost reduction: Gets rid of the need for in-house warehouse space, labour, and equipment.
- Scalability: 3PLs are often experts in picking and packing services, and more adept at handling fluctuations in order volume, ensuring efficient operations during peak seasons.
- Expertise: 3PLs have specialised knowledge and technology to optimise picking and packing processes.
- Improved efficiency: Access to advanced warehouse management systems and automation lead to increased productivity.
- Reduced errors: Experienced 3PL staff minimise picking and packing mistakes.
- Faster delivery: Efficient operations can lead to quicker order processing and shipping times.